Potentiale ausschöpfen –
Warum ein Schweizer Präzisionsfertiger mit einem FFS von Fastems alles richtig macht
Ein Lohnfertiger für Hochpräzisionsteile entschied sich für ein flexibles Fertigungssystem (FFS) von Fastems zur Automatisierung von zwei Fräszentren. Warum das Unternehmen trotz hohem Zeitdruck die Potenziale des Systems von Anfang an voll ausschöpfen wollte und dafür mit einer Reihe an positiven Ergebnissen belohnt wurde, zeigt dieser Erfahrungsbericht.
Die HÖGG-Firmengruppe besteht aus der HÖGG Liftsysteme AG, der simplify engineering AG sowie der HÖGG AG Produktionstechnik. Die Unternehmen agieren als eigenständige Firmen mit insgesamt 180 Mitarbeitern unter dem Dach der HÖGG Holding AG. Kern der Gruppe ist die HÖGG AG Produktionstechnik mit Sitz in Wattwil (Kanton St. Gallen), die sich als Lohnfertiger auf die Fertigung von Hochpräzisionsteilen für verschiedenste Branchen konzentriert. Das Unternehmen sieht sich als Spezialist in der zerspanenden Fertigung, mit Kernkompetenzen u.a. im Drehen, Fräsen, Schleifen und Profilfräsen. Weitere Schwerpunkte liegen in der Montage von Baugruppen und Systemen sowie der Herstellung von Profilen.
„Mit rund 80 Maschinen, darunter zirka 55 CNC-Maschinen, und 105 Mitarbeitern, davon allein rund 85 in der Fertigung, sind wir ein idealer Partner für alle Kunden, die einen Lohnfertiger mit hoher Fertigungstiefe und einem breiten Bearbeitungsspektrum suchen“, sagt Stefan Kaufmann, Co-Geschäftsführer und Fertigungsleiter der HÖGG AG Produktionstechnik.
Mit Automatisierung gegen den Fachkräftemangel
Wie fast alle Lohnfertiger in der Schweiz, hat das Unternehmen mit dem Fachkräftemangel zu kämpfen. „Das ist eine echte Herausforderung, denn wir finden nur sehr schwer qualifizierte Mitarbeiter, die auch bereit sind, im Schichtbetrieb zu arbeiten, wobei sich die Situation in den letzten fünf Jahren noch verschärft hat. Wenn das Teilespektrum passt, kann Automatisierung hier ein Rezept sein, damit die Arbeitszeiten für die Mitarbeiter flexibler werden. Hinzu kommen zudem Investitionen in neue, leistungsfähigere Maschinen“, meint Kaufmann.
2019 investierte die HÖGG AG Produktionstechnik in ein Fräszentrum von Starrag Heckert (HEC 500) zur Bearbeitung von Stahl und plante zusätzlich eine ältere Bestandsmaschine im gleichen Fertigungsbereich durch eine zweite HEC 500 zu ersetzen.
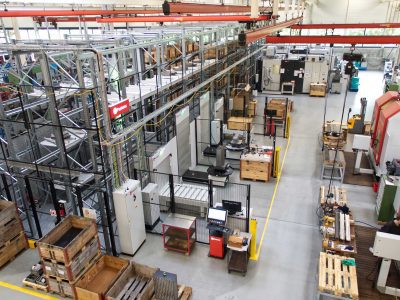
Das flexible Fertigungssystem von Fastems ist seit Februar 2023 bei der HÖGG AG Produktionstechnik in Betrieb.
FFS von Fastems plus intelligente Steuerung
Zur Automatisierung der beiden HEC 500 entschied sich Högg Produktionstechnik für ein FFS von Fastems (FMS One), mit der Option, später eine weitere Maschine hinzuzufügen.
Das FFS bietet mit einer Länge von 36 Metern und einer Höhe von 6 Metern ausreichend Kapazitäten für 68 Maschinenpaletten (500 x 500mm und 500 x 630mm) sowie 96 Materialpaletten und verfügt über je zwei Be- und Entladestationen für Maschinen- und Materialpaletten.
Gesteuert wird das FFS von der Manufacturing Management Software (MMS) von Fastems, einer der derzeit wohl leistungsfähigsten Lösungen zur Planung, Ausführung und Überwachung von automatisierten Prozessen in der spanabhebenden Fertigung. So ermöglicht es die MMS anhand der für verschiedene Aufträge hinterlegten Stammdaten bspw. die Produktion unter Berücksichtigung aller notwendigen Ressourcen (z. B. NC-Programme, Werkzeuge, Rohmaterialien, etc.) automatisch für mehrere Tage im Voraus zu planen.
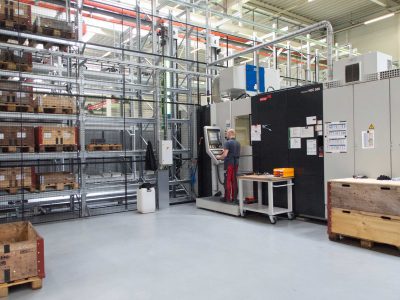
An das System sind derzeit zwei Fräszentren von Starrag Heckert (HEC 500) angebunden, wobei die Option besteht, eine weitere Maschine hinzuzufügen.
Maschinenschaden erfordert schnelle Reaktionen
Geliefert wurde das FFS im Dezember 2022. Parallel zur Montage bereitete man auch die erste HEC 500 für die Anbindung an das System vor. Doch selbst bei bester Planung kann es manchmal anders kommen als gedacht, wie Stefan Kaufmann aus Erfahrung weiß: „Etwa zur gleichen Zeit musste die ältere Bestandsmaschine aufgrund eines Schadens ausgemustert werden. Weil die zweite HEC 500 noch nicht lieferbar war, konnten wir mit Blick auf zukünftige Aufträge nur auf das bereits vorhandene Fräszentrum zurückgreifen, das schon Bestandteil des FFS war. Wir mussten daher quasi von heute auf morgen mit dem System arbeiten.“
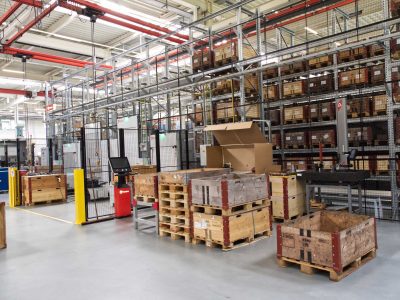
Das FFS bietet Kapazitäten für 68 Maschinenpaletten (500 x 500mm und 500 x 630mm) und 96 Materialpaletten und verfügt über je zwei Be- und Entladestationen für Maschinen- und Materialpaletten.
Trotz hohem Zeitdruck aus der Not eine tugend machen
Bei der Automatisierung mit einem FFS von Fastems besteht die Wahl zwischen einem statischen und dynamischen Routing der Paletten im System.
„Um die Potenziale des FFS von Beginn an richtig auszuschöpfen, entschieden wir uns für ein dynamisches Routing, obwohl wir unter hohem Zeitdruck standen“, berichtet Mathias Schnyder, Bereichsleiter CNC-Stahl 2, und präzisiert:
„Während beim statischen Routing eine bestimmte Reihenfolge zur Abarbeitung der Paletten mit zuvor zugeordneten Maschinen festgelegt wird, ermöglicht das dynamische Routing eine weitaus flexiblere Planung und Steuerung der Produktion. Dies führt u.a. zu einer besseren Rückverfolgbarkeit der Artikel im System, einer höheren Maschinenauslastung und bei Wiederholaufträgen zu deutlich reduzierten Rüstzeiten. Hinzu kommen eine Fülle an wertvollen Produktionsdaten.“
Binnen kurzer Zeit über 300 NC-Programme implementiert
Eine entscheidende Voraussetzung hierfür ist, dass für jeden Auftrag der gesamte Produktionsprozess als Stammdaten in der MMS hinterlegt wird, wozu die Software eine ganze Reihe an Informationen benötigt, z. B. die für einen Auftrag erforderlichen NC-Programme, Werkzeuge, Rohmaterialien, Vorrichtungen sowie Artikelnummern, Zeichnungsnummern, Auftragsnummern etc. „Das ist am Anfang mit einem gewissen Zeitaufwand verbunden, der aber mit zunehmendem Datenbestand geringer wird, weil z. B. einmal in der MMS hinterlegte Vorrichtungen einfach für einen weiteren Auftrag ausgewählt werden können“, erklärt Mathias Schnyder.
Binnen kürzester Zeit wurden rund 330 NC-Programme der älteren Bestandsmaschine eingefahren und in die Stammdaten der MMS mit entsprechenden Anpassungen übernommen. Eine beachtliche Leistung, die fortgesetzt wurde, denn seit Inbetriebnahme des FFS hat sich die Anzahl auf mittlerweile rund 400 Programme, zum Teil für die Mehrseitenbearbeitung, erhöht. „In diesem Zeitraum konnten wir bereits rund 150 bis 200 verschiedene Aufträge mit dem FFS fertigen, zumal in der Zwischenzeit auch die zweite HEC 500 angebunden wurde“, so Schnyder.
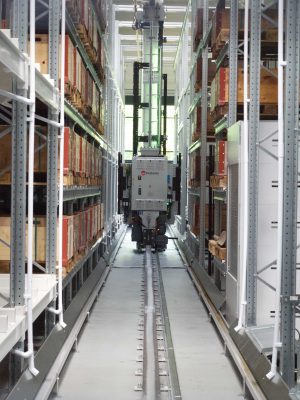
Blick in das 36 Meter lange und 6 Meter hohe System von Fastems mit dem Regalbediengerät.
Rüstzeiten um bis zu 85 Prozent reduziert
Mit dem bisherigen Projektverlauf sind Stefan Kaufmann und Mathias Schnyder angesichts der bislang erzielten Ergebnisse sehr zufrieden. „Da wir einen Anteil von 60 bis 70 Prozent an Wiederholaufträgen haben, konnten wir die Rüstzeiten um bis zu 85 Prozent reduzieren. Besonders bemerkbar macht sich das bei spezifischen Teilefamilien, für die wir eine gewisse Anzahl an Vorrichtungen auf den Maschinenpaletten im System belassen, bis der Fertigungsauftrag erneut kommt und wir nur noch die Werkstücke aufspannen müssen. Die Rüstzeiten für die Maschinen entfallen hier komplett. Das dynamische Routing bietet uns außerdem entschieden mehr Flexibilität, da wir etliche Aufträge nun über beide Maschinen laufen lassen und hierbei einen Materialmix – derzeit Stahl, rostfreie Stähle und Aluminium – bearbeiten können“, betont Stefan Kaufmann.
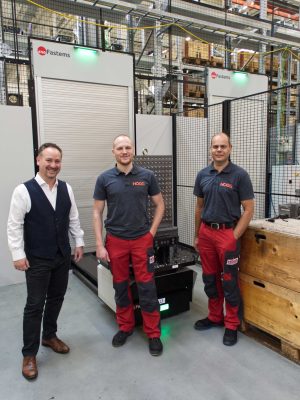
Mathias Schnyder (Mitte), Bereichsleiter CNC-Stahl 2, und Stefan Kaufmann (rechts), Co-Geschäftsführer und Fertigungsleiter, mussten das System binnen kürzester Zeit für die Fertigung fit machen. Gennaro Teta (links), Sales Manager von Fastems für die Schweiz, freut sich über die bisherigen Ergebnisse.
Wertvolle Daten, gezielte Optimierungen und mehr Transparenz
Für Mathias Schnyder sind überdies die über die MMS aus der laufenden Fertigung gelieferten Daten hochinteressant:
„So konnten wir auf Basis solcher Daten bspw. bereits gezielte Optimierungen bei den Werkzeugstandzeiten vornehmen, weil wir jetzt genau sehen, welche Werkzeuge wie häufig im Einsatz sind und daher stärker verschleißen.
Insgesamt ist die Fertigung nun wesentlich transparenter, weil wir nun eine Vielzahl valider Daten haben, etwa zu den Maschinenlaufzeiten und damit Maschinenauslastungen sowie zum Einsatz der Vorrichtungen, um nur wenige Beispiele zu nennen.
Alles wertvolle Informationen, die uns auch die Kalkulationen zu den Aufträgen erleichtern.“
Maschinenauslastung
von bis zu 90 Prozent am Tag
Derzeit wird mit dem FFS in zwei bemannten Schichten produziert. Einige spezifische Aufträge lassen sich zudem in eine mannlose dritte Schicht hinein bearbeiten. „Das geschieht noch nicht durchgängig. Wir nutzen aber jede Gelegenheit, die sich bietet“, meint Stefan Kaufmann und zieht ein positives Fazit:
„Zu berücksichtigen ist, dass wir uns nach wie vor in der Ramp-up-Phase befinden, aber schon jetzt deutliche Vorteile erzielen, wie u.a. an den Rüstzeiten ersichtlich ist. Die Investitionen haben sich auf jeden Fall rentiert, denn das FFS ist eine echte Bereicherung für unsere Produktion, zumal wir schon Tage mit einer Maschinenauslastung von 80 bis 90 Prozent hatten. Derzeit rechnen wir für beide Maschinen mit rund 160 Produktionsstunden pro Woche, wobei wir aber das Fertigungsspektrum für das FFS weiter konsequent ausbauen.“