Hoher Automatisierungsgrad trotz kleiner Losgrößen
Die Vorgabe für eine gesteigerte Produktivität und längere Maschinenlaufzeiten bei gleichzeitiger Haltung einer breiten Palette an Teilevarianzen während der Produktion kann nur durch intelligente Automationskonzepte umgesetzt werden. Die Gebr. Heller Maschinenfabrik GmbH hat eine Lösung für diese Vorgaben gefunden.
Serienfertigung? Nicht bei Heller! 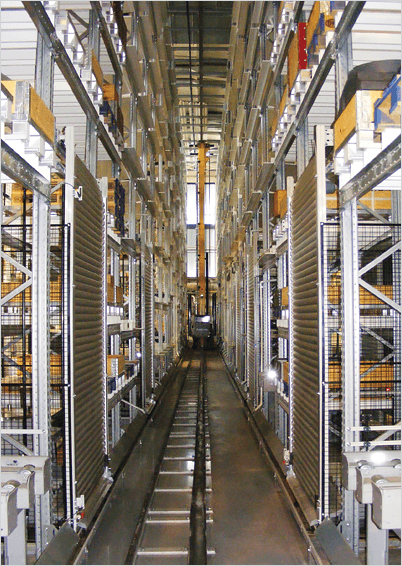
Dr.-Ing. Peter Herrmann (Fertigungsleiter) ist sich sehr wohl bewusst, dass auch ein Unternehmen wie Heller mit Traditionen und damit lang bewährten Montage- und Fertigungskonzepten brechen muss, um diese Ziele zu erreichen. „Wir sind kein Serienhersteller, sondern fertigen unsere Maschinen auftragsnah. Bereits in den Jahren 2006 und 2007 zeichnete sich bei uns eine deutliche Tendenz zur Einzelfertigung bzw. auftragsbezogenen Fertigung ab Als Konsequenz hieraus haben wir 2009 die Losgrößen halbiert. Momentan bewegen wir uns tendenziell bei den wichtigsten Teilen, die vormals bei einer durchschnittlichen Losgröße von sechs bis zehn lagen, nun bei Losgrößen zwischen zwei und drei.
Kernkompetenz wurde bewahrt
Zu diesen „wichtigen Teilen“ zählen die sogenannten „Kompetenzteile“, beispielsweise Spindelmaschinen, Maschinenpaletten, Drehtische und Teile des Werkzeugwechslers. „Die Fertigung solcher Komponenten muss mit einer sehr hohen Genauigkeit erfolgen und stellt daher hohe technologische Anforderungen an die Produktion. Wir wollten insbesondere in diesem Bereich leistungsfähig bleiben, damit wir die erforderlichen Teile rechtzeitig zur Verfügung stellen können.“
Leistungsfähig zu bleiben, bedeutete für Claus Garnjost und Peter Herrmann eine komplette Umstrukturierung der Fertigung und damit eine höhere Automatisierung bei größerer Flexibilität.
Längere Maschinenlaufzeiten
Markus Schwirzinger (Projektleiter Fertigung) beschreibt, was damit konkret gemeint ist: „In unserer Fertigung befanden sich einige Maschinen, die nur mit Palettenwechslern oder Palettenpools ausgestattet waren. Uns war klar, dass wir mit dieser Maschinenausrüstung unsere Vorstellungen einer effizienteren Produktion nicht erreichen konnten. Außerdem wollten wir höhere Maschinenlaufzeiten mit weniger Maschinen erreichen und gleichzeitig das Personal effizienter einsetzen, damit wir schneller auf den Bedarf unserer Montage und somit auf Kundenwünsche reagieren konnten. Wir
haben relativ schnell erkannt, dass hierfür eigentlich nur ein flexibles Fertigungssystem wie das Multi-Level-System (MLS) von Fastems in Frage kommt, das auch den bislang ungenutzten Raum in der Hallenhöhe ausschöpfen kann und uns eine im hohen Maße flexible Fertigung ermöglicht.“
Herausforderungen meistern
Bevor jedoch das System installiert werden konnte, waren viele Vorbereitungen erforderlich. „Es ist keine einfache Aufgabe, 50 Maschinen umzusetzen, um den benötigten Platz von ca. 900 Quadratmetern für das komplette System zu schaffen, während die Produktion in einem kompletten Drei-Schichten-System weiterlief“, erinnerte sich Claus Garnjost. Selbst der Deckenkran musste aufgrund der Höhe des Systems verschoben werden. Die größte Herausforderung bestand jedoch darin, den Werkboden zu stabilisieren. An der vorgesehenen Aufstellungsstelle des MLS wurde eine Straßenbaumaschine eingesetzt, die die Aufgrabung des Bodens durchführte, damit das neue Fundament und ein neuer Boden errichtet werden konnten. „Dies alles wurde innerhalb kürzester Zeit erledigt, sodass wir den Zeitplan für die Lieferung und Installation des FMS von Fastems einhalten konnten“, fügt Claus Garnjost hinzu..
Optimale Raumnutzung
Trotz all dieser Probleme wurde das Multi-Level System (MLS) von Fastems plangemäß im September 2008 installiert. Das MLS‑XMD (Extra Medium Duty) von Fastems bietet genügend Raum für insgesamt 256 Maschinenpaletten und 134 Materialpaletten. Das System verfügt über eine Tragkraft von 2500 kg und weist eine Länge von 46 m und eine Höhe von 11 m auf.
Zwei MCH280-Bearbeitungszentren sowie zwei MCH350-Bearbeitungszentren von Heller sind derzeit an das MLS angebunden. Für die größeren Maschinen stehen 116 Paletten (800 × 800 mm) mit einem Maximalgewicht von 2.500 kg zur Verfügung. Weitere 140 Maschinenpaletten (630 × 630 mm) mit einem Maximalgewicht von 1.500 kg sind für die beiden MCH280-Zentren reserviert. Das System ist so ausgelegt, dass es durch zwei weitere Bearbeitungszentren erweitert werden kann. Aufgrund der verstellbaren Gabeln kann das Regalbediengerät des MLS beide Palettengrößen handhaben.
5000 geplante Stunden
„Auf einer Fläche, auf der sich zuvor sieben Bearbeitungszentren befanden, stehen jetzt nur noch vier Maschinen. Wir können uns den vergleichsweise großen Flächenverbrauch des Gesamtsystems leisten, denn mit diesen vier Maschinen erreichen wir eine wesentlich höhere Produktivität. Wir hoffen, jährlich ca. 5.000 Betriebsstunden pro Maschine bei einem Drei-Schichten-System zu erreichen. Wir erreichen dies, indem wir die Arbeitsvorbereitung und Stillstandzeiten von der tatsächlichen Arbeitszeit der Bearbeitungszentren trennen. Im Vergleich dazu erreichten wir im vergangenen Jahr bis zu 3.500 Stunden pro Maschine, wobei jede Stunde auch eine Mannstunde war“, so Peter Herrmann.
Parallele Vorbereitung und Verarbeitung
Darüber hinaus sieht Claus Garnjost mit dem neuen System einen deutlich positiven Effekt für eine Effizienzsteigerung in der mechanischen Fertigung. „Die parallele Vorbereitung und Verarbeitung sind hier Schlüsselbegriffe. Im Grunde bedeutet dies ein intelligentes Automationskonzept, bei dem die Verarbeitung von Rohmaterial und Fertigteilen auf effiziente Weise kombiniert wird. Auf der einen Seite haben wir das MLS mit vier Bearbeitungszentren und insgesamt fünf Ladestationen für eine optimale Beladung der Maschinen. Auf der anderen Seite steht uns im System auch das Rohmaterial zur Verfügung. Neben den Ladestationen befinden sich vier Rollenförderer, die das Rohmaterial zum Beladen bereitstellen, sowie ein fünfter Rollenförderer, der für die Zuführung des Rohmaterials in das MLS sorgt.“
Intelligenter Puffer
Während die Maschinen arbeiten, können die Bediener an den Ladestationen die verschiedensten Teile aufspannen. Dabei ist es irrelevant, wann die Teile bearbeitet werden, da die Leitsteuerung den internen Materialfluss steuert und der Maschine das Material zum benötigten Zeitpunkt bereitstellt. Der Speicher dient somit als Puffer zwischen dem Ladevorgang und der Bearbeitung, sodass die Bearbeitungszentren im Grunde parallel laufen können. Und noch einen weiteren Vorteil sieht Claus Garnjost: Zum Aufspannen der Werkstücke ist kein hochqualifiziertes Personal mehr erforderlich. „Das bedeutet, dass wir bei der Personalplanung flexibel bleiben können, d. h., die am System derzeit beschäftigten acht Mitarbeiter können auch in einem Drei-Schichten-System eingesetzt werden.“
Extrem hoher Grad an Flexibilität
Mit dem MLS-XMD von Fastems hat eine neue Philosophie in der mechanischen Fertigung bei Heller Einzug gehalten: stabile, mannlose (oder zur Hälfte bemannte) Fertigungsprozesse anstelle von schneller Bearbeitung. „Unsere Bearbeitungszentren werden nicht bis an ihre möglichen Produktionsgrenzen getrieben. Stattdessen legen wir unseren Schwerpunkt auf einen stabilen, sicheren und zuverlässigen Fertigungsprozess. Unter anderem sparen wir durch die längere Werkzeuglebensdauer Kosten ein“, erklärt Peter Herrmann, der insbesondere den hohen Grad an Flexibilität in der Produktion begrüßt. „Ich beschäftige mich mit Systemen dieser Art seit mehr als 30 Jahren. Dies ist jedoch das erste Mal, dass ich ein automatisiertes System sehe, das nach einer Startphase zweihundert unterschiedliche Teile fertigen kann. Genau das können wir dank des MLS von Fastems erreichen.“
Optimierte Effizienz
Claus Garnjost ist davon überzeugt, dass der Kauf des MLS die richtige Entscheidung war. „Das gesamte System ist für einen hohen Grad an Effizienz optimiert. Auch wenn wir aufgrund der globalen Finanzkrise bisher nicht das komplette Potenzial ausschöpfen konnte, stellen wir jetzt nach der Markterholung einen Anstieg der Aufträge fest. Dieser positiven Entwicklung kann dank der Vorteile, die das System hinsichtlich Produktivität und Flexibilität bietet, gelassen entgegengesehen werden. Die Niederlassung wird in Zukunft starke Fluktuationen zunehmend bewältigen müssen. Durch unser Automationskonzept sind wir gut dafür gerüstet.“
Related products:
Was können wir für Sie tun?
Rufen Sie uns an oder senden Sie uns einfach eine kurze Nachricht.