Produktivitätsschub
für die Präzisionsfertigung
ZEISS setzt auf ein flexibles Fertigungssystem von Fastems
ZEISS bietet seine Fertigungsleistungen neben den eigenen Sparten auch externen Kunden an, wobei neben der hohen Produktqualität attraktive Preise gefordert sind. „Diese Anforderungen lassen sich unter anderem mit einem Plus an Automatisierung erreichen“, erklärt Felix Horlacher, Projektleiter Mechanics bei ZEISS am Standort Oberkochen. „Wir haben die Erfahrung gemacht, dass das beispielsweise mit dem Flexiblen Fertigungssystem (FFS) von Fastems gut funktioniert“.
ZEISS ist ein weltweit führendes Technologieunternehmen der optischen und optoelektronischen Industrie. Das Unternehmen ist in den vier Sparten Semiconductor Manufacturing Technology, Industrial Quality & Research, Medical Technology und Consumer Markets tätig. Ein Fertigungsbereich von ZEISS ist unter anderem für die Produktion, Montage und Belieferung des Unternehmens mit mechanischen und optischen Bauteilen zuständig – so werden in der mechanischen Fertigung in Oberkochen beispielsweise Tuben für hochwertige Filmkameraobjektive produziert.
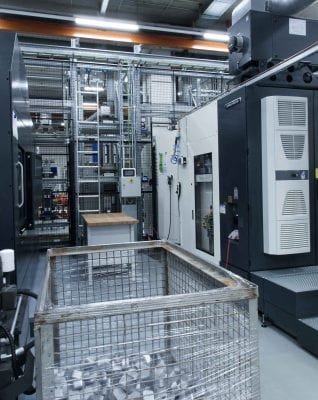
Auch auf eng bemessener Produktionsfläche lässt sich eine gleichsam effiziente wie hochproduktive Automation realisieren, wie das MLS von Fastems zeigt.
Mehr Produktivität pro Quadratmeter
In der Fertigung sind vor allem Effizienzsteigerung und eine hohe Produktivität, u.a. durch Automatisierung, stets aktuelle Themen.
Insbesondere die Flächenproduktivität sei in diesem Zusammenhang nach Aussagen von Horlacher ausschlaggebend, denn Produktionsfläche ist aufgrund der gegebenen baulichen Bedingungen rar.
Produziert wird auf zwei Ebenen.
Für die Serienproduktion stehen rund 2.500 Quadratmeter zur Verfügung, wobei zirka 2.500 verschiedene Bauteile, größtenteils in Serien mit Losgrößen von 20 bis 200, gefertigt werden.
Aufträge unter Losgröße 20 sind hingegen typische Aufgaben für die Produktion im Obergeschoss, in der sich unter anderem die Prototypenfertigung befindet.
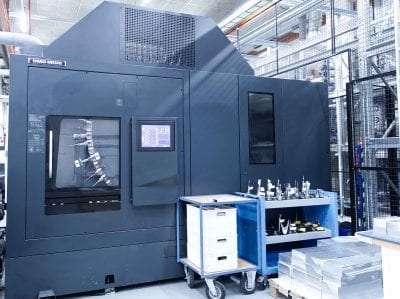
In einem ersten Schritt wurde im Jahr 2017 die erste DMC 60 HL mit einem Fassungsvermögen von 243 Werkzeugen an das MLS gekoppelt. Ein baugleiches BAZ konnte schließlich knapp zwei Jahre später an das System angebunden werden.
Investitionen mit
höherer Fertigungsflexibilität
Auch auf eng bemessener Produktionsfläche lässt sich eine gleichsam effiziente wie hochproduktive Automation realisieren, wie Horlacher aus Erfahrung weiß: „Als wir in ein horizontales 5-Achs-Bearbeitungszentrum investiert haben, wollten wir auch das Palettenhandling der Maschine automatisieren“.
In dem Zusammenhang hatte sich ZEISS zunächst ganz bewusst für eine DMC 60 HL entschieden, weil diese Maschinentypen bereits in der Fertigung eingesetzt werden – allerdings mit 63 Werkzeugplätzen, während das Magazin der Neuinvestition mit Blick auf eine höhere Fertigungsflexibilität über 243 Werkzeuge fassen sollte.
FFS mit Option für Erweiterungen
Flexibel wollte ZEISS aber auch bei der Automationslösung selbst bleiben. Und hier fiel die Wahl auf ein FFS von Fastems, genauer auf ein Multi-Level-System (MLS) vom Typ MD (Medium Duty) mit einer Tragkraft pro Palette von 750kg. Überzeugt habe das MLS-MD vor diesem Hintergrund vor allem, weil es von Beginn an für eine bedarfsorientierte Erweiterung mit zusätzlichen Maschinen ausgelegt werden konnte und sich überdies sehr flexibel in die vorgesehene, eng begrenzte Produktionsfläche integrieren lies. „Hinzu kommt, dass das System, anders als andere Lösungen, auf zwei Seiten Paletten aufnehmen kann, was die Anzahl der möglichen Palettenplätze auf engstem Raum entscheidend erhöht“, so Horlacher.
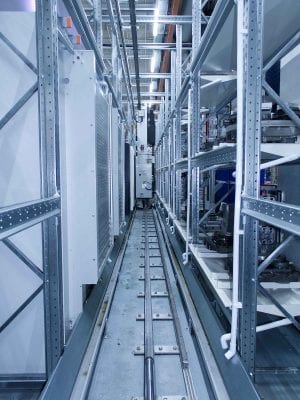
Das MLS mit einer Länge von 28 Metern und einer Höhe von knapp vier Metern bietet Platz für insgesamt 55 Maschinenpaletten, wobei selbst der Platz über den Be- und Entladestationen ausgenutzt wurde.
Sukzessiver Ausbau mit Maschinen
Das MLS mit einer Länge von 28 Metern und einer Höhe von knapp vier Metern bietet Platz für insgesamt 55 Maschinenpaletten und integriert zwei Be- und Entladestationen.
In einem ersten Schritt wurde im Jahr 2017 die erste DMC 60 HL an das MLS gekoppelt, in dem sich zunächst knapp 30 Maschinenpaletten befanden.
Die Bestellung der zweiten, baugleichen Maschine mit identischer Anzahl an Werkzeugplätzen erfolgte rund ein Jahr später und konnte schließlich 2019 an das System angebunden werden.
Analog hierzu wurde die Anzahl der Paletten auf insgesamt 55 aufgestockt. Die Spanntürme verfügen über maximal 20 Werkstückplätze und ermöglichen, falls erforderlich, eine durchgängige Fertigung mit Mehrfachaufspannungen für die Erst- und Zweitbearbeitung auf einer Vorrichtung.
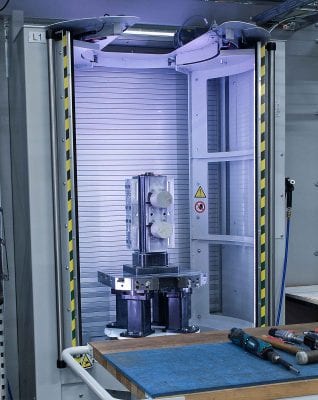
Über die beiden integrierten Be- und Entladestationen wird das System mit Rohmaterialien versorgt und die Fertigteile ausgeschleust.
Hohe Automation trotz kurzer Bearbeitungszeiten
Derzeit befinden sich rund 30 verschiedene Materialnummern im System, wobei die Anzahl der unterschiedlichen Bauteile, vorwiegend aus Aluminium, kontinuierlich ausgebaut wird. Die Bearbeitungszeiten pro Bauteil bewegen sich zwischen wenigen Minuten bis hin zu einer Stunde. Aufgrund der potenziell hohen Anzahl an Aufspannungen pro Vorrichtung, lassen sich jedoch selbst bei kurzen Bearbeitungszeiten relativ lange Maschinenlaufzeiten erzielen.
Während der Fertigung selbst sind höchste Präzision und Prozesssicherheit oberstes Gebot. Ein Grund, warum man u. a. ausnahmslos auf Paletten vom Maschinenhersteller setzt. Somit kann auf ein Nullpunkt-Spannsystem als weitere Schnittstelle z. B. zu einer neutralen Palette verzichtet werden, was sich laut Horlacher auch in der Genauigkeit der Zerspanung bemerkbar macht.
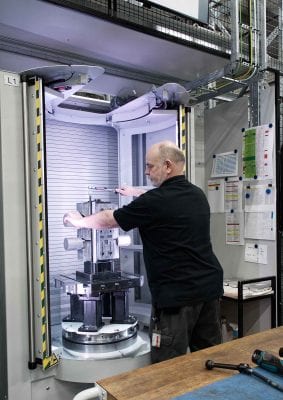
Produziert wird im Dreischicht-Betrieb mit bemannter Früh- und Spätschicht sowie zusätzlicher unbemannter Nachtschicht, wodurch die Fertigungskosten zusätzlich reduziert werden.
Flexible Produktion mit
nachhaltigen Kostensenkungen
„Mit dem FFS können wir viele unterschiedliche Teile auf zwei Maschinen hocheffizient und flexibel produzieren. Während der Tagschichten benötigen wir jeweils nur einen Mitarbeiter, der sich um die Aufspannungen und das Be- und Entladen kümmert. Da wir hierdurch die Personalkosten pro gefertigtes Bauteil nachhaltig senken, sind wir in der Lage, wesentlich kostengünstiger zu produzieren“, unterstreicht Horlacher.
Produziert wird im Dreischicht-Betrieb mit bemannter Früh- und Spätschicht sowie zusätzlicher unbemannter Nachtschicht, wodurch sich die Fertigungskosten nochmals reduzieren.
„Und bei Bedarf fertigen wir auch am Wochenende mannlos, indem wir mit einem entsprechenden Produktionsplan das System für die hochautomatisierte Produktion bis in den späten Sonntag hinein vorbereiten.“
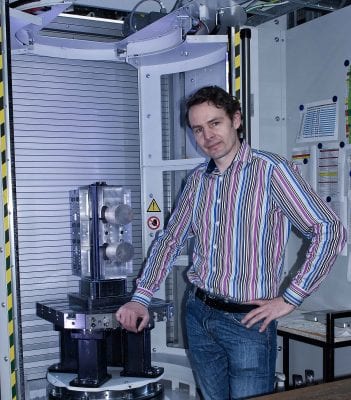
Felix Horlacher, Projektleiter Mechanics bei ZEISS in Oberkochen: „Unsere Produktivität hat sich durch die Automationslösung nahezu verdoppelt.“
Ambitionierte Vorgaben mit hohen Erwartungen
Mit Blick auf die Investition in das MLS von Fastems gab es seitens ZEISS schon von Beginn an eindeutige Vorgaben hinsichtlich der Produktivitätserwartungen.
Felix Horlacher erinnert sich: „Die erste Maschine sollte pro Woche mindestens auf eine Laufzeit von 140 Stunden kommen, bei insgesamt 168 möglichen Produktionsstunden. Diese Vorgabe konnten wir mit dem FFS auch tatsächlich erreichen und teilweise sogar übertreffen.“
Für den Projektleiter steht daher die Produktivität der Lösung außer Frage, zumal es hierfür weitere Belege aus der Praxis gibt: „Wir hatten an der Stelle, an der sich nun das FFS befindet, zwei BAZ, ebenfalls von DMG Mori, die konventionell im Drei-Schicht-Betrieb bedient wurden. Mit dem System von Fastems und nur einer angebundenen Maschine haben wir bereits die gleichen Spindellaufzeiten erzielt, die wir zuvor mit den beiden erwähnten BAZ erreichten.“
Produktivität nahezu verdoppelt
So ist es im Grunde nicht überraschend, dass die mechanische Fertigung allein mit einer der beiden am MLS gekoppelten Maschinen im letzten Jahr auf über 6.000 Spindelstunden kam.
Entsprechend positiv ist das Fazit von Felix Horlacher:
„Unsere Produktivität hat sich durch die Automationslösung nahezu verdoppelt. Zusätzlich zu den Einsparungen bei den Personalkosten haben wir den Durchsatz bei gleichzeitig verkürzten Rüstzeiten und geringeren Fertigungskosten pro Stück deutlich erhöht.“