Produktivität im Doppelpack
Flexible Roboterzelle automatisiert zwei Werkzeugmaschinen
Dem Ziel einer hochflexiblen, automatisierten Produktion trotz vergleichsweise kleiner Lose und hoher Teilevarianz ist die Buck CNC Technik entscheidend näher gekommen. Das Unternehmen fertigt eine Vielzahl verschiedener Produkte aus zwei Teilefamilien mit einer RoboCell ONE von Fastems, an der zwei Dreh-Fräszentren angebunden sind.
Die Buck CNC Technik GmbH, seit Anfang 2020 zu 100 Prozent im Technologieverbund der Hydraulik Nord Group (siehe Kasten), fertigt als Komplettanbieter im Bereich der Zerspanung u.a. Maschinenbauteile für Werkzeugmaschinen, Elektro- und Verbrennungsmotoren, Getriebe, Hydraulik und Baumaschinen. Das Unternehmen mit Sitz in Dürmentingen (Landkreis Biberach, Baden-Württemberg) erzielte 2019 mit etwa 90 Mitarbeitern einen Umsatz von zirka 14 Mio. Euro.
„Auf rund 6.000 Quadratmetern Produktionsfläche werden vor allem Guss und Stahl verarbeitet, wobei wir bei den häufig wiederkehrenden Teilefamilien Stückzahlen von zirka 100.000 pro Jahr erreichen. Die Losgrößen bewegen sich hierbei je Auftrag zwischen 100 und 1.000 Stück, mit Werkstückgewichten von einigen hundert Gramm bis 200 kg“, erklärt Helmut Wöhr, Geschäftsführer der Buck CNC Technik.
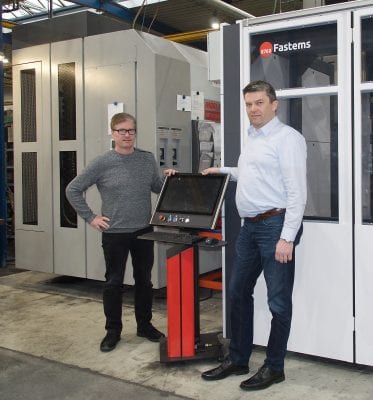
Helmut Wöhr (links), Geschäftsführer der Buck CNC Technik, und Produktionsleiter Frank Emmerich sind mit den Ergebnissen der RoboCell ONE zufrieden und wollen mit der Lösung weitere Potenziale heben.
Optimierungspotenziale stets im Blick
Produziert wird im flexiblen Schichtsystem, je nach Auftragsvolumen mit bis zu drei Schichten. Darüber hinaus wird seit jeher konsequent auf Automatisierung gesetzt.
So investierte Buck vor rund 18 Jahren erstmals in eine Roboterzelle. Bereits zuvor verfügte schon ein Großteil der CNC-Maschinen über Palettenpools. Seit 2008 ist außerdem ein flexibles Fertigungssystem von Fastems mit über 1.000 Maschinen- sowie Materialpaletten im Einsatz.
Hohe Produktivität ist was Feines. Dennoch sind Optimierungspotenziale stets ein Thema, wie Produktionsleiter Frank Emmerich nur zu gut weiß: „2017 entschlossen wir uns zur Investition in ein Dreh-Fräszentrum G220 von Index mit Gegenspindel, um spezifische Gussgehäuse, die wir zuvor auf einer Fräsmaschine in zwei Aufspannungen produzierten, komplett fertigen zu können. Hierbei handelt es sich um verschiedene Produkte einer Teilefamilie, für die wir zum Be- und Entladen der Maschine außerdem eine Roboterlösung suchten.“
Da die Bearbeitungszeiten je nach Bauteil zwischen 12 und 16 Minuten betragen, lag es aus Sicht von Emmerich nahe, eine Bestandsmaschine, genauer eine Mori Seiki NT4300 DCG, ebenfalls mit Gegenspindel, zur Fertigung ähnlicher Gussteile in eine Automationslösung zu integrieren, um den Roboter optimal auszulasten.
„Mit der RoboCell ONE haben wir schließlich die ideale Lösung hierfür gefunden“, so der Produktionsleiter.
Automationslösung
für schwere Werkstücke
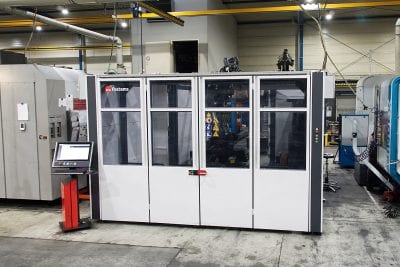
Passt selbst in Fertigungsumgebungen mit eng bemessener Produktionsfläche: Die RoboCell ONE präsentiert sich mit 6 x 4 m Grundfläche als platzsparende Automationslösung.
Die RoboCell ONE von Fastems wurde speziell für die flexible Losgrößenfertigung mit hoher Teilevarianz entwickelt und ist zur Automatisierung von bis zu zwei Werkzeugmaschinen für die Handhabung vor allem von schwereren Werkstücken bis 80 kg ausgelegt. Der auf einer Linearachse verfahrbare Roboter versorgt somit zwei Maschinen flexibel mit Werkstücken, wobei die Möglichkeit besteht, auf beiden Maschinen parallel unterschiedliche Produkte zu fertigen.
Hierzu Frank Emmerich: „Derzeit produzieren wir mit der Roboterzelle zwei Teilefamilien mit jeweils fünf variierenden Produkten auf der Mori Seiki NT4300 DCG und 20 verschiedenen Bauteilen auf der Index G220. Die Rohteile schleusen wir auf Transportwagen mit Rasterplatten in das System, wobei für jede Maschine zwei Wagen mit jeweils 40 Werkstücken bereitstehen. Ein zusätzlicher Wagen ist zudem zur separaten Ablage von Prüflingen reserviert.“
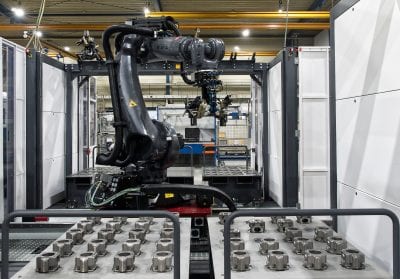
Die Rohteile für die Fertigung befinden sich auf Transportwagen mit Rasterplatten. Pro Maschine stehen zwei Wagen mit insgesamt 40 Werkstücken für die Bearbeitung bereit.
Nebenzeiten verkürzen
Zur Handhabung der Roh- und Fertigteile für beide Maschinen nutzt der Kuka-Roboter je einen Doppelgreifer, den er bei Bedarf automatisch über die integrierte Greiferwechselstation aufnimmt bzw. ablegt. „Erfolgt innerhalb einer Teilefamilie ein Werkstückwechsel mit veränderten Bauteildimensionen, rüstet ein Mitarbeiter den entsprechenden Greifer manuell über ein Schnellverstellung um.
Das ist eine Sache von nur wenigen Minuten“, erklärt Emmerich und betont: „Hinsichtlich der Gesamtproduktivität der Roboterzelle fallen auch die Nebenzeiten für das Umrüsten einer Maschine zunächst nicht ins Gewicht, da mit dem jeweils anderen Dreh-Fräszentrum in einem solchen Fall prinzipiell weiter produziert werden kann. Allerdings produzieren wir mit unterschiedlichen Maschinen verschiedene Teilefamilien und müssen mit Blick auf die Umrüstzeiten unsere Strategien entsprechend anpassen.“
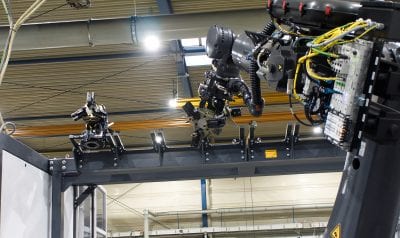
Der Roboter von Kuka nimmt automatisch den für das Materialhandling jeweils erforderlichen Doppelgreifer aus der Greiferwechselstation, die mit Blick auf eine hochflexible Werkstückhandhabung für die Aufnahme von insgesamt acht Greifern ausgelegt ist.
Das Magazin der Bestandsmaschine verfügt über 102 Werkzeugplätze und hat damit eine ausreichende Anzahl an Tools zur Fertigung der fünf variierenden Produkte. Nur alle zwei bis drei Tage sei laut Emmerich bei einem Produktwechsel das Umrüsten der Spannbacken erforderlich. Das auf der Index gefertigte Produktspektrum ist allerdings weitaus breitgefächerter, wodurch sich die Komplettbearbeitung aller Werkstücke mit den insgesamt 118 Werkzeugplätzen trotz doppelt besetzbarer Drehwerkzeuge nicht bewältigen lässt. „Somit müssen wir bei einem Produktwechsel mitunter auch die Werkzeuge umrüsten. Wir versuchen aber, ähnliche Teile in Folge zu fertigen, um hier ebenfalls die Nebenzeiten entscheidend zu verkürzen“, so der Produktionsleiter.
Plus an Intelligenz für die Produktionsplanung
Ein zentraler Bestandteil der RoboCell ONE ist die Manufacturing Management Software (MMS) von Fastems. Die MMS ist in der Lage, entsprechend der Produktionsaufträge automatisch die gesamte Fertigung mit wechselnden Werkstücken in unterschiedlichen Losgrößen und unter Berücksichtigung sämtlicher hierfür benötigten Ressourcen zu planen. Die Software zeigt zudem den Status der aktuellen Fertigung in Echtzeit an (Auftragsfortschritt, Zeitplan, etc.), kalkuliert die Maschinenkapazitäten für noch anstehende Aufträge und visualisiert dem Bediener bereits im Voraus notwendige Maschinenumrüstungen.
„Momentan legen wir die Aufträge für die Produktionsplanung noch manuell in der MMS an, die auch die Stammdatenverwaltung der Bauteile übernimmt. Zukünftig wollen wir aber die Aufträge direkt aus unserem ERP-System an die MMS übertragen“, erklärt Frank Emmerich und unterstreicht vor allem die Vorzüge der Software im Hinblick auf die Roboterprogrammierung.
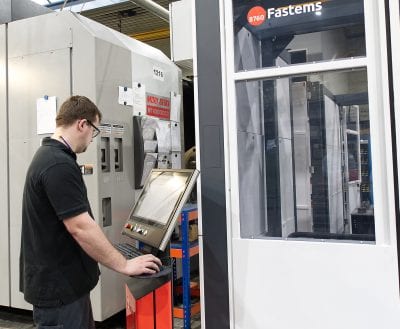
Roboterkonfiguration ohne Programmierkenntnisse. Mit der parametrischen Programmierung lassen sich die Verfahrwege des Roboters einfach und schnell definieren.
Keine Roboterkenntnisse erforderlich
Statt den Roboter bei einem Neuauftrag zeitaufwendig einzuteachen, erfolgt dessen Konfiguration mittels parametrischer Programmierung über die MMS.
Hierzu sind keinerlei Roboterkenntnisse erforderlich, wie der Produktionsleiter bestätigt:
„Wir haben eine Schulung erhalten und anhand von zwei konkreten Musterteilen gelernt, wie das in der Praxis funktioniert. Anschließend konnten wir in sehr kurzer Zeit die Roboterkinematiken für die weiteren Produkte selbst festlegen. Hierzu müssen wir im Grunde nur einige wenige Referenzwerte bzw. Parameter eingeben oder entsprechend modifizieren, um die Verfahrwege des Roboters zum Be- und Entladen in der Zelle zu definieren. Das geht wirklich sehr schnell und reibungslos ohne zusätzliche Programmierkenntnisse.“
Verdopplung der mannlosen Zeiten im Visier
Aus Sicht von Geschäftsführer Helmut Wöhr hat sich die Investition in die RoboCell ONE vor mehr als einem Jahr auf jeden Fall gelohnt:
„Das war eine richtige Entscheidung, denn nun sind wir in der Lage, insgesamt 25 verschiedene Bauteile aus zwei unterschiedlichen Teilefamilien mit zwei Dreh-Fräszentren in einer einzigen hochautomatisierten Roboterzelle gleichermaßen flexibel wie wirtschaftlich zu fertigen.
Auf diese Weise realisieren wir mit der Index eine Jahresstückzahl von rund 20.000 Teilen. Mit der Mori Seiki kommen wir aufgrund der vergleichsweise längeren Bearbeitungszeiten für die Bauteile immerhin auf bis zu 14.000 Fertigteile pro Jahr und Teilefamilie. Produziert wird hierbei in mehreren Schichten und minimalstem Personaleinsatz, wobei wir momentan außerdem über einen Zeitraum von drei bis vier Stunden rund 15 verschiedene Bauteile gänzlich unbemannt fertigen können. Unser Ziel ist es aber, diese Zeitspanne nahezu zu verdoppeln, sodass wir auf eine komplett mannlose Schicht kommen.“